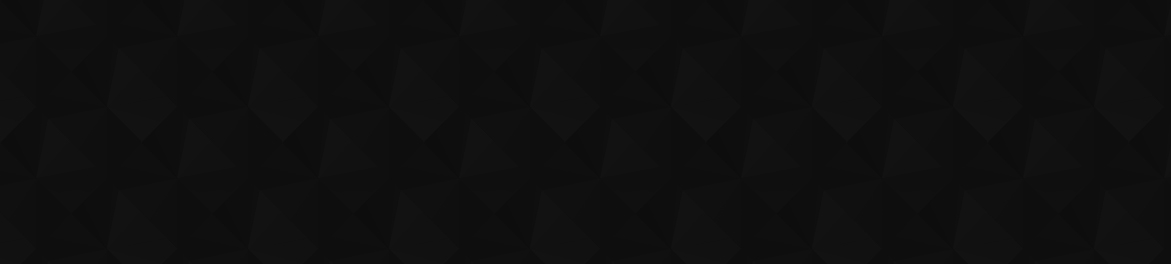
- 12
- 500 970
Reiner Schmidt
Canada
Приєднався 4 жов 2011
Korad KWR103 KWR102 Review and General Info
Korad KWR103 KWR102 Review and General Info
Переглядів: 4 685
Відео
3D Printed Mars Rover Conquers Banana
Переглядів 2,1 тис.4 роки тому
Hello all. This is the first robot design of 3. I am working on some other designs that I will be posting soon. If you guys want to give some feedback I would love to hear about it in the comments. - do you like the setup for the video? - is the assembly of the robot interesting? More to come! Subscribe to see it all.
20 Amp Discharge Test on Lithium-Ion 18650 with a Korad KEL103
Переглядів 13 тис.5 років тому
This video covers a use case of DC electronic loads. The load is used to test the battery capacity at different discharge rates. Software Library - github.com/Mango-kid/py-korad KEL103 - www.sra-shops.com/korad-kel-103-programmable-dc-electronic-load-300-watt-low-ripple 18650 HG2 - www.ebay.ca/itm/2PCS-LG-HG2-18650-3000mAh-20A-High-Drain-Rechargeable-Battery-Flat-Top/283379849796?hash=item41fac...
Bridge Boy: OS 5 Axis (mostly) 3D Printed Mill
Переглядів 135 тис.6 років тому
This is the first video of Bridge Boy, an Open Source 5 Axis CNC mill. This video covers the head build. 3D Model - a360.co/2vcl9jl Stepper Motor Driver -vroboteurs.com/products/slushengine-raspberry-pi-hat-stepper-motor-driver
RobotRock E#0: Robot Bin Locating
Переглядів 2,9 тис.6 років тому
The bad video quality will stop. Just need to get something better than my cellphone and a web cam :S
Vison Guided Bin Picking
Переглядів 1,3 тис.6 років тому
arm locks at the end because I parked the robot to far away
Rooibos OpenPNP V1.0
Переглядів 19 тис.7 років тому
My first OpenPnP build. Has a lot of issues but works well with 0603 at slow speed.
3D Printed 6 Axis. First test
Переглядів 317 тис.7 років тому
Built with this kit: roboteurs.com/products/rbx1-remix-3d-printed-6-axis-robot-arm-kit This robot was built using only a 3d printer, no machining of any components was required. The robot uses only a Raspberry Pi and SlushEngines to control the robot, and external computer is not required. Driver board: roboteurs.com/products/slushengine-model-d I have been working with Roboteurs in hopes to of...
Electronic EGR Control: McMaster Btech Electronics Lab
Переглядів 1,7 тис.10 років тому
This is a demonstration using Freescalers automotive controllers to implement PID motor control functionality. There is an variable inductor inside the EGR mechanism that allows us to determine the position. The PID runs at 400Hz with error checking.
Solenoid Engine: McMaster Btech Manufacturing Lab
Переглядів 1,5 тис.10 років тому
This engine/motor uses solenoids to move pistons up and down. It was created for the 3MP3 manufacturing technologies course.
HAZMAT Robot - McMaster University Btech
Переглядів 1,4 тис.11 років тому
This Robot was designed and built by Engineering students at McMaster University. The robot is designed to go into hazardous areas and asses the environment. The robots capabilities include: - Temperature sensing - Smoke detecting - Carbon monoxide level monitoring - Audio and Video feedback to the user The main idea of this project was to develop a versatile and low cost robot that would attra...
MSP 430 Accelerometer Meets Hobby Servo
Переглядів 1,2 тис.12 років тому
In this demonstration an accelerometer is used to move a hobby servo. The angular position of the hobby servo is determined by the acceleration of gravity as it effects the x axis of the acceleromter.
how do you test the battery and get the graph (in the software)? i dont have any info on this procedure and need it for work related things. this would be very helpful thanks in advanced
Soo cool. Any update on this in action ?
The battery's are fake
G'day, I've just ordered one of these Tenma/Korad loads. Couple of points. I would have used 4 wire mode to measure the real battery voltage as the "only 10mOhms" in one lead gives you 20mOhms between the 2 and 400mV drop at 20A so that will impact any calculations you are using that involve voltage. You discharged those poor cells way below the accepted / recommended limits of ~2.7-3.0V so I guess your capacity test will not really reflect what you would get in a real world application as you should not be abusing the cells like that! With the amount of heating you are seeing (45C at 2.8v @ 5A) it is clear they are not designed for long high discharge cycles and you may encounter thermal runaway if you used them in such an application. Cheers. -- Edit just realised this video is old...
Great project. Thanks for sharing. What software do you suggest?
this project died ? or there is a machine done with this head ?
Did you made any progres with this project or any one tried this on real machine ? As nema17 isnt a strong mottor
You could always make the gripper using a smaller stepper motor OR use pneumatics.
Дякую
Hi May I ask why you did not use the battery test setting ?
What is the length of the belt? It's not in the drawing.
Great video. Thanks for review!
where can we get the files (cad or stl) for this robot arm?
Fiber glass mesh
hi rainer, have you finish your 5 axis project.. look very interesting to build this too Gruss Jürgen Raschke
There’s more UHMM… AHMM than electrons, here
Reiner were you able to get the LAN control working? I can't seem to find any instructions for that 🤦♂
As far as I remember you need to use there software or the USB connection to enable it in DHCP mode or set an IP address. It was a funky process, but the software on the CD helps.
@@MrReinerMSchmidt I will try that, thanks!
@@MrReinerMSchmidt My question is the same. Now I have the IP address of the power supply, but there is no documentation on how to control it. Does it use TCP or UDP?
Did you finish it?
Dear Reiner, I came across your interesting video because I'm looking for an electronic load. I'm oriented to buy the kel103 vs the ET5410A+ as the price difference in Europe is not very high. The last one seems to have more features like CC+CV or CR+CV LED and so on but the Korad is more accurate and robust. Do you know if the Kel103 can have the same features programming it with python? Thank you
Yes it can be programmed with python. I have done some automated battery testing with it. It has lots of features but there may be a small accuracy difference in the ET5410As favor.
@@MrReinerMSchmidt Thank you!
Your measurement of the voltage accuracy (around 8:30 ) is flawed. Your test leads are pretty thin + travel through 2 connectors. If you assume that the KWR103 and your voltmeter are 100% accurate, you get a resistance of 50 mOhm for the connection. According to Ohms Law, this resistance is the reason for your lower measured voltage at 1 Amp (-0,05 V), 5 Amp (-0,25 V) and 15 Amp (-0,75 V)
Yeah, realized that I didn't have the sense leads on the back connected either. Hopefully redo this video eventually.
Im curious about why you named this project BridgeBoy. Brandon Sanderson fan?
For all who are interested in this nice peace of psu: do not compare apples with oranges. The (left) KA3005P/6003P is a linear one with core transformer and linear regulation, whereas the shown KWR is a switching psu with all benefits and disadvantages. If you are about charging batteries, consider a switching psu because of its way better efficiency. Doing some repairs in analogue or digital circuits I would always recommend a linear psu as Reiner does. Finally, it's better to have two different for differenct use cases instead of a one who should fit all. If you do not need >30V, have a look on the 102, it delivers 30A up to 10V (from 15A@20V to 10A@30V they're both equal). jm2c.
I spent a few hours to reverse-engineering the video and F360-models to make the project more "Open-Source", so if someone willing: V-axis bearing is "6009-zz (5972K271)", U-axis bearing is "6210-2RS (5972K366)", The pulley are "1428N420_T5 SERIES TIMING BELT PULLEY" The U-belt is MEGADYNE MPW2 T5 400 3017, the V-axis belt I can't find, the video not clear about it same as at the 3D model... Hope I helped you a little 😆 Best regards, Linda 😇
thanks!
@@MrReinerMSchmidt yw! Btw, it will be awesome if you help us with the belt and pulley naming, i think we are good enough to know this XD
@@MethelinaPills I'm going to look through some old notes. I couldn't find the belts in my order history but from the CAD I can reverse calculate them.
@@MrReinerMSchmidt Cool, thx, it will help!
Im torn between the KWR103 and 6005P. Which one is better? (I need it to drive LEDs with 42V and debug power circuits in laptops/as a psu for notebooks) Would love to hear from you! ❤
If your just driving LEDs and don't need the clean feed the 6005P offers, you will get a lot more power out of the KWR.
What happened with this project?
pls show use of cr mode
Hi, I assume the script you wrote is in Python? I assume I copy and paste the file into notepad?
This power supply is driving me crazy...just using it for 28vdc charging of batteries. The dislpay jumps all over the place but when measured with a DVM the voltage is stable. Can't figure out the settings to get the display to reflect the output. Any ideas?
Wow Awesome , This is cool , looking forward to add this to my cnc machine...
I like your creative design for 5-axis milling head, but I am not a big fan of timing belts. They can be very precise solution, but it won't handle any force in material. Try using PLANETARY REDUCTOR insted of timing belts.
Hello Reiner, my first bench PSU will be this Korad KWR103 or the famous Korad KA3005P. Which do you recommend, which is better in your opinion?
What will you be doing with it? For analog electronics the KA3005P is the best option for sure. But if you are doing some heavier stuff the other is better. I have a couple ka3005p and 60v versions that have been in use with no issues for almost 10 years. The KWR I have only had since this video, but no problems thus far.
@@MrReinerMSchmidt I want to start a repair business (Macbooks, iPhones, iMac) and I'm thinking about which one would fit my needs better to power them on a budget
@@limebulls ah I see. Well I'm not heavy into laptop repair so I'm not sure the needs. But I would say if it is being used to debug smaller circuits on the laptop then you are probably fine with the KA3005P, I think you can get two of them for the price of one of the other units and for what you are doing having multiple sources might suit you better.
this is a moveo copy
Correct! But modified to have a 6th Axis
Hello Reiner, did you shared somewhere V1 or V2 files? currently planning to build myself one and checking out different designs to combine fot mine.
pravo
Just downloaded model, those bearings will have running clearance?
Hi, I'd use several RND KEL102 (same looking) load device with aligned load stepping. There is a "trigger" connector on the back, but not a single word about it in the datasheet. Do you know how to use trigger input? Logic level, or opencollector/drain to short to trigger? How fast load switching can be (I'd load LDO power supplies)? Any info on that would be appreciated:))
Honestly I am not to sure. The trigger does work as an enable button. I would guess that the response rate can be determined by watching the load ramp up with a scope. I would guess it's at least 60Hz.
2:32 P= U x I Power supply Korad KWR103 =(60V/15A), 300W ;-) 60vx15a=900 But We have 300W et voilà it's a Swing to one side! You can sew 5 and 10 hats from one skin, and the essence is not in the hats, but in the size. I prefer one Well in size!
If anyone has built this I'd be interested in having a discussion or looking for a good forum to chat online. I've downloaded the CAD files but it would be good to speak with others and get a sense of any updates/gotchas since the 2018 release of this video. Reiner's info has not been readily available online but it seems that he may be on to newer projects at this time. Thanks.
Hanzhen harmonic drive gear , machine gear reducer, over 30 years experience , robot gear
très bien réaliser mais je doute sur la solidité en usinage je travaille aussi sur mon projet de 5 Emme axe mais en aluminium
This is amazing! This is really high quality work! Are you still developing this? I don't mean to make you feel any pressure or anything... I am just really excited! I can't wait to hear from you!
Amesome design Reiner! any updates so far on this?
I modified these files as you suggested. Printed in PETG, I found straight 1.78A rms NEMA 17's to skip steps, so went with a 5:1 planetary. Using Dynomotion Klfop board and software to handle the kinematics. Just test cuts so far in foam but seems to be promising. Once roadworthy will machine a foam main body and do lost -foam casting. My belts seem a hair loose for some reason so added some ultra "custom" tensions. Maybe a redesign to build in tensioners? idk, anyway thanks again for getting the design out there!
ua-cam.com/video/DF6puTm5a_8/v-deo.html here is the test kinematics video
awesome work! could you please share the modified files :)
Reiner, Do you perhaps know when there will be more stock of the SlushEngine: Model D Stepper Motor Driver. I'd like to buy one. Is it possible to have a Stepper Motor Driver that connects to USB instead of the GPIOs?
very nice , i like your job ,any chance to share drawing pls .. ?
Nice video ,very cool project,im building my CNC combo using Rack & Pinion drive .. :) for sure i want to build head like yours but of Alu. Thanks for file ..!! ua-cam.com/channels/NmOINTaJ1jUHMGe7ql2bQg.html